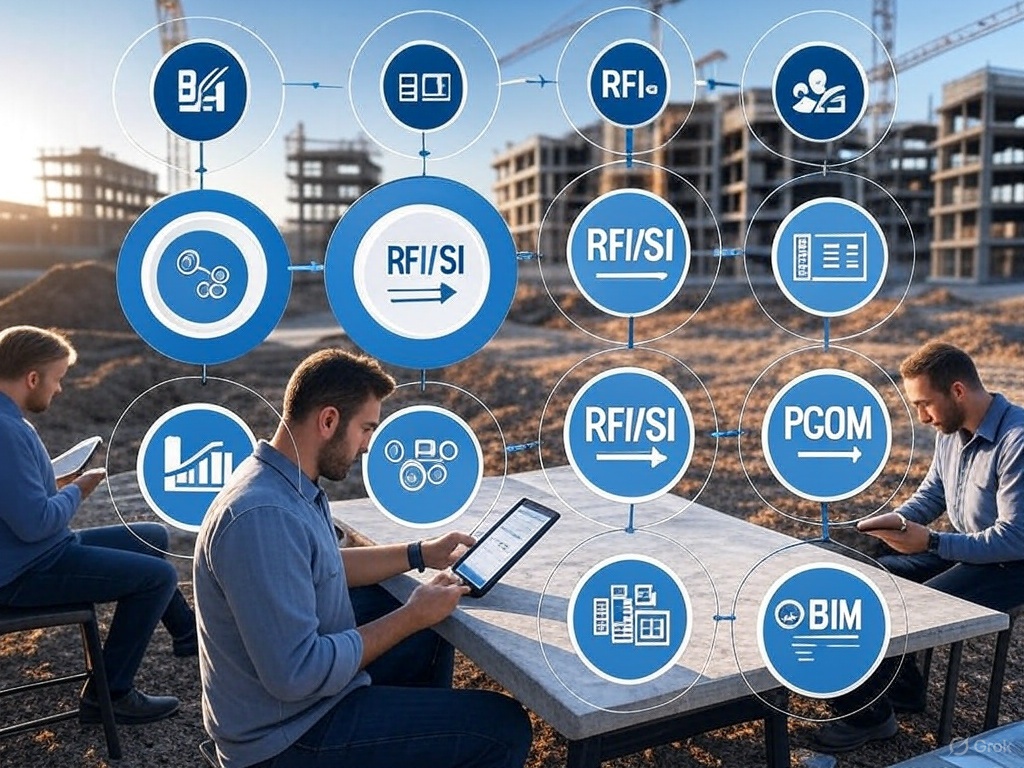
The dynamic interplay between RFIs, SIs, PCOs, and COs underscores the need for robust, technology-driven workflows in contract administration . In the fast-paced world of construction, effective communication and documentation are vital to ensuring projects stay on track. Central to this process are Requests for Information (RFIs), Supplemental Instructions (SIs), Proposed Change Orders (PCOs), and Change Orders (COs), which together form a critical workflow for addressing uncertainties, resolving discrepancies, and adjusting project scope, cost, and timelines. However, inefficiencies, potential misuse, and manual processes often complicate this workflow, leading to delays, disputes, and increased costs.
This expanded article delves deeper into the RFI process, its challenges, and how integrated technology, combined with proactive strategies, can streamline transitions while empowering architects, consultants, and project teams to maintain control and drive successful outcomes.
The RFI Workflow: From Clarification to Cost Adjustment
RFIs serve as a formalized mechanism for stakeholders—such as contractors, or subcontractors—to request information that isn’t readily available through research or existing project documentation. Though not explicitly defined in standard Canadian Construction Documents Committee (CCDC) contracts, RFIs are a cornerstone of construction communication. They are typically initiated during the design or construction phase to address ambiguities, discrepancies, or missing details in contract documents, such as architectural drawings, specifications, or Building Information Modeling (BIM) models. For example, a contractor might submit an RFI to clarify whether a specified concrete mix meets the compressive strength requirements outlined in ACI 318-19, or to confirm dimensional tolerances for a prefabricated facade panel per ASTM standards.
When an RFI highlights a need for clarification, the architect, often with input from consultants like structural or mechanical engineers, responds. If the clarification doesn’t affect the project’s cost or timeline, the response is issued as a Supplemental Instruction (SI). SIs are directives that provide additional guidance, such as specifying an alternative installation method or addressing unforeseen site conditions like poor soil stability that requires adjusted foundation work. However, if the SI or RFI response reveals a need for changes—such as upgrading structural steel sections (e.g., from W14x90 to W14x120 to meet ASCE 7-22 load requirements) or rerouting HVAC ductwork due to a clash with underground utilities—a Proposed Change Order (PCO) is initiated. The PCO documents the proposed adjustments, including revised cost estimates, material quantities, labor hours, and schedule impacts. Once approved by the relevant stakeholders, typically the owner and architect, the PCO becomes a Change Order (CO), formalizing the change in the project’s scope, budget, or timeline.
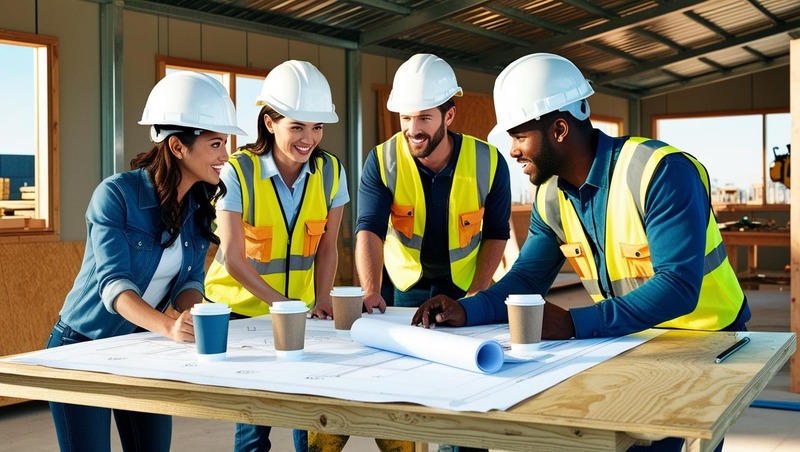
This workflow ensures that all parties remain aligned, but it requires meticulous attention to detail. For instance, an RFI might reveal that a design oversight necessitates additional rebar to comply with seismic requirements, impacting not only material costs but also the project schedule due to resequencing of concrete pours. Similarly, an SI addressing utility conflicts might require new materials, such as additional ductwork or piping, and could lead to delays if subcontractors need to be remobilized. Properly managing these transitions is critical to maintaining project momentum and avoiding costly disputes.
Challenges in the RFI Process: Misuse and Inefficiencies
Despite its importance, the RFI process can be a double-edged sword. Contractors sometimes misuse RFIs by submitting excessive or frivolous requests, which can strain project timelines and relationships. Common reasons for this behavior include:
- Avoiding Due Diligence: Contractors may find it easier to ask the architect for clarification rather than thoroughly reviewing contract documents, even when the information is readily available.
- Shifting Responsibility: RFIs can be used to transfer accountability for a contractor’s errors or omissions to the architect, such as claiming a design flaw when the issue stems from improper execution.
- Justifying Claims: Contractors might imply non-existent errors or omissions in the documents to support claims for additional work, such as requesting compensation for “unforeseen” conditions that were actually documented.
- Delay Tactics: The RFI process can be exploited to create circumstances that support unjustified delay claims, such as submitting high volumes of RFIs to argue that responses were untimely.
- Discrediting Consultants: Excessive RFIs may be used to undermine the architect’s or consultant’s competence, portraying them as unprepared while emphasizing the contractor’s expertise.
For example, a contractor might submit an RFI requesting confirmation of a detail already specified in the drawings, set an unreasonably short response time (e.g., 24 hours), and then claim a delay if the architect doesn’t respond promptly. In extreme cases, contractors may issue RFIs for previously answered questions or use high volumes to build a case for a delay claim, creating friction between project stakeholders.
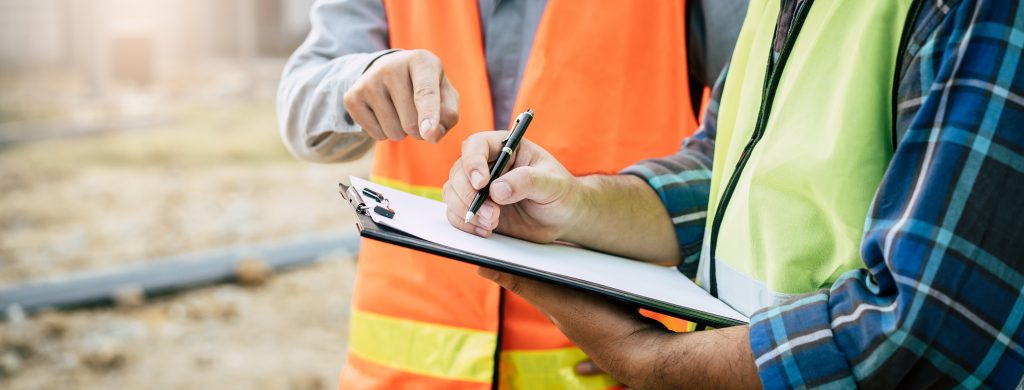
Beyond misuse, the technical process of converting RFIs and SIs into PCOs introduces additional challenges. Traditional workflows are often manual, requiring project teams to extract data from RFIs or SIs—such as revised material quantities, updated drawings, or cost breakdowns—and re-enter it into separate PCO forms. This manual approach leads to several inefficiencies:
- Data Redundancy: Re-entering details like RFI numbers, material specifications, or cost estimates increases the risk of errors, such as transposing numbers or omitting critical information.
- Loss of Context: Disconnected systems often fail to link RFI or SI metadata (e.g., originator, date, or referenced drawings) to the PCO, making it difficult to trace the origin of a change during audits or disputes.
- Delayed Approvals: Manual handoffs between project management, engineering, and accounting teams can stall PCO processing, delaying approvals and impacting cash flow or construction schedules.
These inefficiencies can have a cascading effect. For instance, a delayed PCO approval might hold up the procurement of additional materials, causing subcontractors to demobilize and increasing costs due to downtime. Similarly, errors in cost estimates due to manual data entry can lead to budget overruns, eroding trust between stakeholders.
Strategies for Effective RFI Management
To mitigate these challenges, architects and consultants can adopt a combination of proactive strategies and best practices to manage RFIs effectively and maintain control over the process. Implementing these strategies can help architects and consultants not only manage RFIs more effectively but also reduce the risk of disputes and delays, ensuring the process serves the project’s goals rather than hindering them.
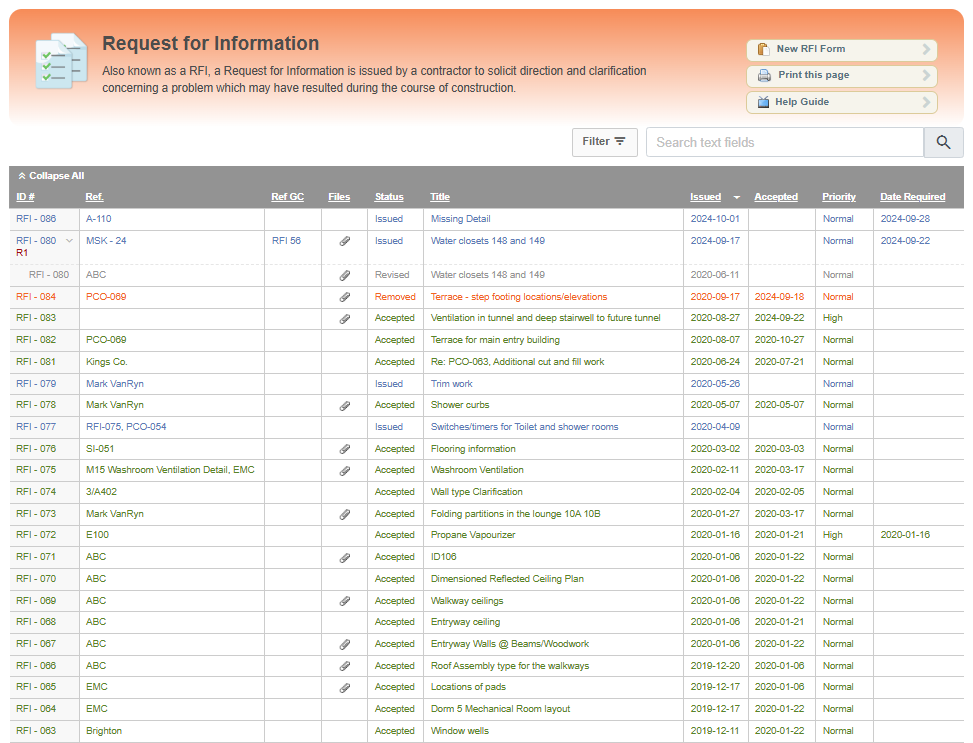
- Define the Process in the Contract: Since RFIs aren’t formally defined in CCDC contracts, include a clear definition in Supplementary Definitions and Conditions, supported by a Division 01 specification section outlining the process, roles, and expectations.
- Discuss Early and Often: Use the pre-construction meeting to establish RFI procedures, discuss the use of standard forms, and set expectations for communication. Encourage ongoing dialogue by dedicating time (e.g., 30 minutes) during regular site meetings for queries, which can reduce the need for formal RFIs.
- Evaluate Impact Thoroughly: Assess whether an RFI response warrants an SI or a PCO. If it does, reference the related SI or PCO number in the response and issue it simultaneously to maintain clarity and avoid miscommunication.
- Use Professional Forms or Disclaimers: Respond to RFIs on your own professional form to maintain consistency and control. If forced to use a contractor-provided form, include a disclaimer to avoid inadvertently agreeing to unreasonable terms, such as statements implying the response will affect cost or schedule.
- Push Back on Frivolous RFIs: For unnecessary or repetitive RFIs, return them promptly with a request for clarification, using stamps to reference existing drawings or specifications. Avoid delays in responding, as they may legitimize the RFI and associate the architect with project delays.
- Resolve RFIs Individually: Treat each RFI as a standalone issue, closing it out once answered. Avoid letting RFIs become ongoing dialogues or a series of follow-up questions. If a question is repeated, refer to the original response to maintain efficiency.
- Track Response Times Carefully: While CCDC contracts don’t mandate specific response times, contractors may designate desired timelines. The CCDC 2 contract stipulates that contractors “shall not proceed with the work affected” until they receive the necessary information, so respond promptly to prevent delays while avoiding rushed answers that could lead to errors.
- Maintain Independent Records: Keep a detailed RFI log with dates received and answered, titles, descriptions, relevant document numbers, and comments. This protects you if you lose access to the contractor’s database or need to challenge its accuracy during a dispute.
- Address RFI Abuse with Contractual Measures: Add a Supplementary Condition to the CCDC 2 General Conditions, allowing architects to invoice the client for additional administrative costs if a contractor issues excessive unnecessary RFIs (e.g., after five are identified as frivolous). These costs can be charged to the contractor as a credit on subsequent Certificates for Payment, handled as a CO.
- Stay Vigilant and Proactive: Recognize that RFIs are initiated by contractors and may be used strategically to their advantage. Perceptions during the project can shift dramatically if a claim arises, so document all interactions carefully and maintain a professional, proactive stance.
Streamlining with Technology: RFI to PCO Conversion
Modern contract administration platforms, such as RForm, offer a powerful solution to the inefficiencies of manual RFI-to-PCO workflows enabling seamless, direct conversion of RFIs and SIs into PCOs, minimizing errors and delays. Key features of these platforms include:
- Metadata Preservation: Automatically carry forward RFI and SI attributes—such as issue descriptions, referenced documents, originator details, and dates—into the PCO, ensuring traceability and reducing the risk of data loss.
- Streamlined Approval Workflows: Route PCOs through predefined approval processes, notifying stakeholders via email or dashboards and reducing turnaround time. This is particularly critical for fast-track projects where delays can have significant downstream effects.
- Enhanced Auditability and Compliance: Maintain a digital audit trail linking RFIs, SIs, and PCOs, which is essential for dispute resolution, forensic analysis, or compliance with standards like ISO 9001 for quality management or FIDIC contract terms.
The benefits of such technology-driven workflows are significant and measurable:
- Reduced Administrative Overhead: Automation can save hours per change event, a critical advantage on large projects with hundreds of RFIs. For instance, a project with 500 RFIs might save 1,000 hours of administrative work over its lifecycle.
- Improved Accuracy and Consistency: Preserving technical context—such as linking PCOs to specific drawing revisions or 3D model elements—reduces errors in cost and scope adjustments, ensuring all parties are aligned.
- Faster Decision-Making and Approvals: Real-time integration with project management dashboards allows stakeholders to review and approve PCOs quickly, minimizing delays in procurement or subcontractor mobilization.
- Enhanced Transparency and Accountability: A unified digital record supports compliance with regulatory frameworks, facilitates forensic analysis in claims or disputes, and ensures all actions are documented for future reference.
Beyond these benefits, technology also fosters collaboration by providing a centralized platform where all stakeholders—architects, contractors, owners, and consultants—can access the same information. This reduces miscommunication, builds trust, and ensures that changes are implemented smoothly.
The Bigger Picture: A Holistic Approach to RFI Management
The RFI workflow doesn’t exist in a vacuum—it’s part of a broader ecosystem of construction administration that includes scheduling, cost control, quality assurance, and risk management. Poorly managed RFIs can ripple through a project, causing delays in critical path activities, inflating budgets, and eroding stakeholder relationships. Conversely, a well-managed RFI process, supported by technology and proactive strategies, can enhance project efficiency, reduce risks, and improve outcomes.
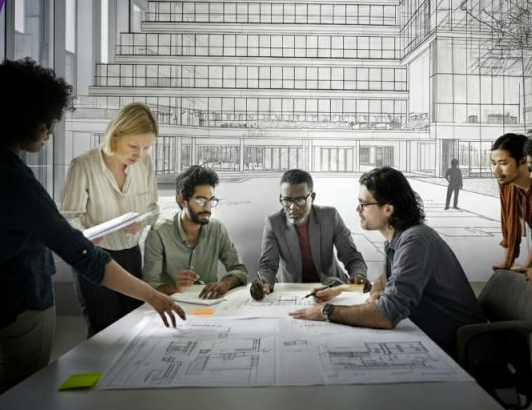
Conclusion
The dynamic interplay between RFIs, SIs, PCOs, and COs underscores the need for robust, technology-driven workflows in construction project management. By combining proactive strategies—such as defining processes, encouraging communication, and addressing misuse—with modern tools that streamline RFI-to-PCO conversion, project teams can navigate this critical process with greater efficiency and control. The result is a reduction in errors, delays, and disputes, paving the way for successful project delivery. As the construction industry continues to embrace digital transformation, mastering the RFI workflow will remain a cornerstone of effective project management, ensuring clarity, collaboration, and cost control in even the most complex projects.